The rapid transition from the benchtop to commercial production is crucial for a successful market launch, return on investment and to fully capitalise on the patent timeline.
To achieve this, Glatt takes a flexible and modular approach to engineering. Predefined modules and proven layouts can be used to achieve “right-first-time” plant design.
Every pharmaceutical or biotechnology project starts with the engineering phase: once the fundamental requirements of the process have been clarified and the initial plant concept has been drawn up, the next step is to confirm the Basic Design. This includes
- the process design
- the control and automation
- the equipment arrangement plan or layout (Figure 1)
- the building/structure to be erected (Figure 2)
- etc.
So far, so good, but which concept should the client choose? Glatt works closely and systematically with each customer to find the right answer.
Concept design: how the process is implemented in principle
Once the synthesis parameters of the manufacturing process have been defined in the laboratory, the concept phase begins. Here, the operational requirements are defined and the implementation of the process strategy — in terms of plant and layout — is determined.
For this purpose, long before detailed piping and instrument diagrams (P&IDs) are drawn up, graphically prepared schematics or process flow diagrams are used to define material flow principles and any necessary links between the unit operations.The transition to the basic design phase then takes place; the specifications and dimensions of the required apparatus are outlined and recorded in the equipment list (among other parameters).
Regarding the final arrangement of the equipment and layout, good manufacturing practice (GMP) aspects and the building floorplan play decisive roles: which areas belong to which hygiene zone, for example, and how are these classified in terms of ventilation and cleanroom class?
Where are the technical areas located and how can certain zones be combined and arranged to save space?
For the production of APIs, in particular, the entire synthesis pathway must be considered as part of the process train. Often, several synthesis steps with different process parameters are done sequentially in the same equipment.
At the same time, the overall sequence may not always run chronologically and/or linearly and could include separate cycles and/or side branches. As such, certain dependencies might arise owing to equipment occupancy or cleaning cycles, which reduce the overall efficiency of the plant.
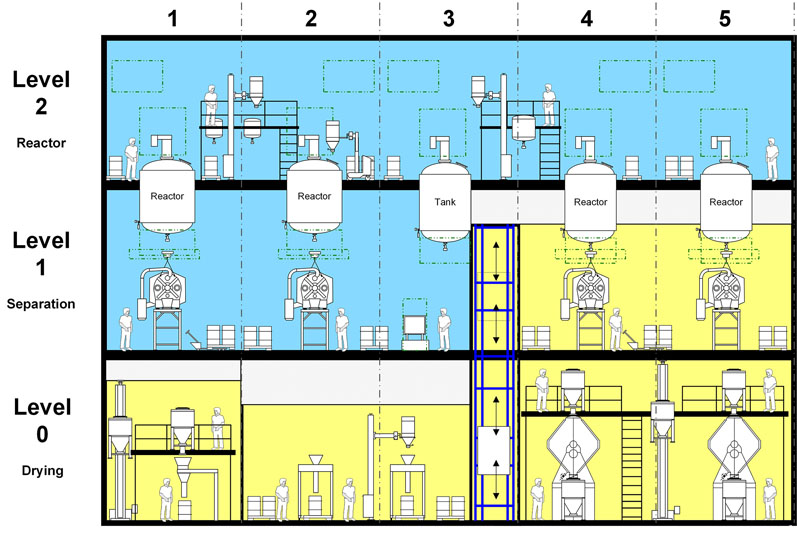
Figure 1: In the functional layout concept, the block areas are finally mapped out with the actual equipment in place; existing layout modules are used for facilities producing active ingredients by chemical sysnthesis (© Glatt)
For an optimal design, it is crucial to identify limitations and bottlenecks in the process flow at an early stage and to take appropriate countermeasures in terms of planning (occupancy).
If, for example, process analysis shows that there will be bottlenecks in the crystallisation step of the synthesis, this can be accommodated with a second crystallisation tank. The efficiency and annual output of the subsequent production line will increase accordingly.
Characteristics of API chemical synthesis
Batch processing still dominates API synthesis because it’s easier to control the thermodynamic and kinetic parameters of the chemical reactions involved.
The annual production quantities of APIs and, specifically, highly potent APIs (HPAPIs) are often quite small; but, these processes have very specific material requirements in terms of reactors, pipes and seals.
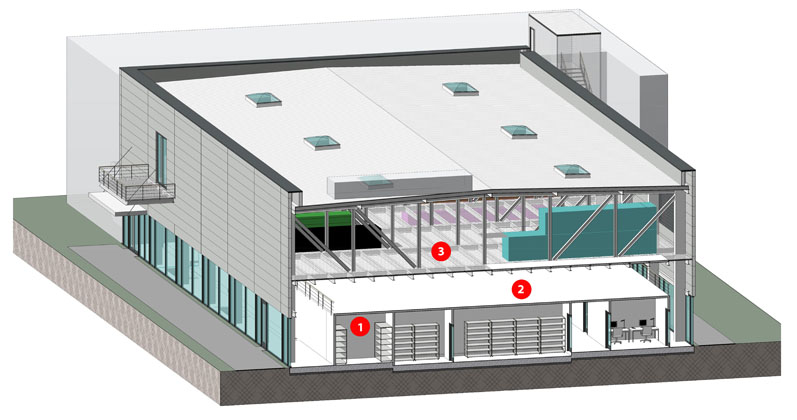
Figure 2: A layout with a deliberately decoupled building structure enables parallel flexibility in the different levels of use of new biotech and pharmaceutical factories: 1 = cleanroom, 2 = walkable cleanroom ceiling, 3 = air handling units and technical level (© PBM Architects)
In addition, the reactants and catalysts involved often have different aggregate states, which makes dosing and mixing more difficult. The scale-up of API synthesis also sometimes poses particular challenges that require modification of the apparatus type, plant layout or process design.
The GMP requirements, safety measures (such as explosion protection), containment/cleanroom and HVAC requirements will vary for different compounds and synthesis steps … and need to be planned and considered for each individual API or HPAPI.
Water-based cleaning, for example, is often not possible or effective: solvents or special chemicals have to be used, which makes plant operation even more challenging.
It is essential to avoid product or cross-contamination with minute amounts of HPAPIs, which are often analytically undetectable or very difficult to distinguish and can lead to unexpected side-effects.
Train concept versus modular system planning
The separation of individual synthesis steps into parallel, independently operating process trains is often preferred in single-product facilities. Successive stages of the “train” can only be started when the required quality of the intermediate product has been analytically confirmed.
Separate synthesis trains have several advantages: the type and size of the plant can be specifically optimised for certain reaction volumes, material properties and individual reaction times. In addition, plant layout issues and the elimination of bottlenecks caused by particular plant components can be solved independently.
Containment measures also only need to be implemented when required. Likewise, cleanroom design — as well as ventilation and air-conditioning — can be dealt with separately in accordance with GMP.
Figure 3: In a functional diagram, the necessary process steps of the planned API synthesis — as well as hygiene requirements regarding material and personnel flow — can be clearly structured in accordance with GMP (© Glatt)
The necessary Health, Safety and Environment (HSE) measures can also be implemented much more effectively. The supply, disposal and handling of products and by-products is often shared and can be operated more economically as independent modules.
However, these advantages also incur higher investment and operating costs for a production environment that’s not very flexible. Here, a modular approach offers a good alternative.
The modularisation of API synthesis
Modular multiproduct facilities for API synthesis not only make it possible to produce several different products for a lower investment, they can also be planned and delivered in a shorter timeframe because the engineering effort is much lower and field-proven solutions are used.
As such, API production becomes more flexible because production capacities can be configured and scaled as required. For example, chemical reaction modules of different designs and sizes can be combined as needed with the appropriate process modules or purification and separation steps.
The required connections are made using preconfigured pipe connectors and/or via flexible (metal) hoses with inliners or coatings.
The modular approach simplifies maintenance, which means that synthetic processes can be optimised and adapted to new requirements by selecting suitable modular connections.
This flexibility goes hand in hand with the fact that the modular plant is not predicated for a specific API in terms of design, size and utilisation. Strict cleaning procedures are essential to eliminate cross-contamination in modular API plant.
Precisely defined Standard Operating Procedures (SOPs) minimise the risk of operating errors and ensure the prevention of product contamination.
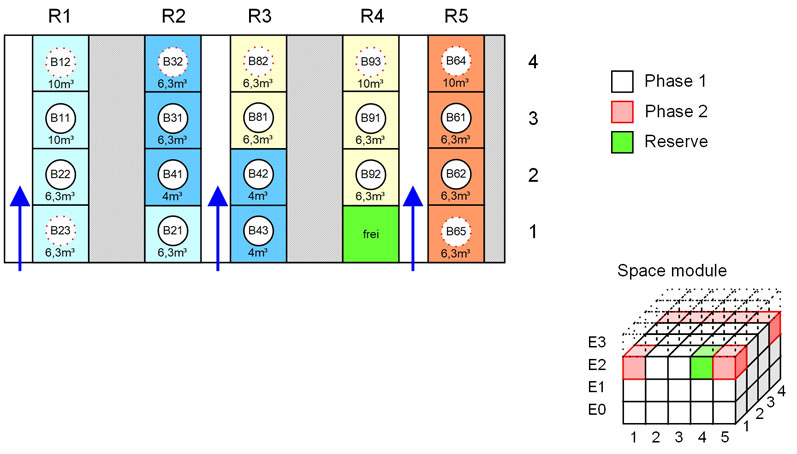
Figure 4: Using typical layouts, a quick estimate of the space requirements can be derived; in addition, possible spatial arrangements of the modules can be simulated (© Glatt)
Design principles for modular plant layouts
At Glatt, the creation of a modular plant for API production follows a standardised procedure. The first step is to define the design principles; these include the technological requirements, the required capacities and any expansion options (in the form of spatial reserves).
GMP requirements, hygiene zoning and the separation of GMP and technical areas also need to be considered. The layout concept, equipment location and personnel/material flows, as well as access for maintenance and cleaning, are all recorded.
The engineering work sequence is executed according to checklists.
A functional diagram (Figure 3) is then determined according to the relevant ISPE guidelines, the applicable regulations and GMP zoning. This results in fairly typical arrangements of process units, operational areas and specifications for personnel and material flow.
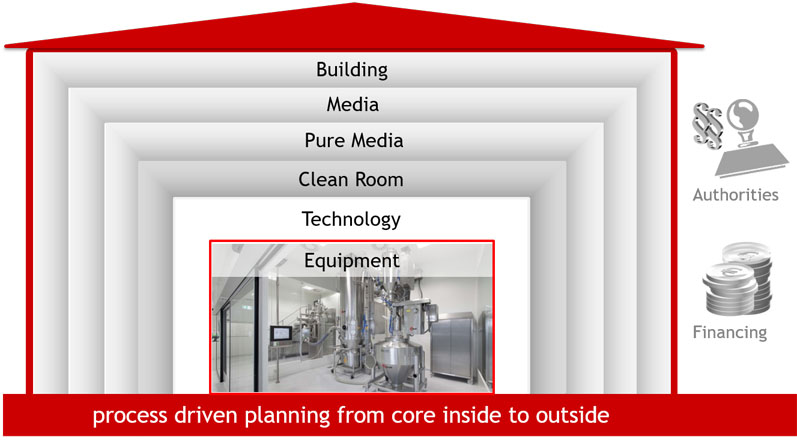
Figure 5: After assessing the production process, Glatt plans all the engineering work for each project — including the integrated layout of the plant, supply, cleanroom fittings and any necessary building (© Glatt)
Layouts from previous projects or suppliers can easily be repurposed and/or modularised to create a library of “ideal blocks.” From the electronically available data of these optimised functional units (layout modules), a quick estimate of the space requirements can be derived.
In addition, the potential arrangement of the functional units can be reviewed, which helps to finalise the spatial block layout of the facility (Figure 4) and provide a sensible basis on which to plan the building and determine its dimensions.
In the functional layout concept, the block areas are finally mapped out with the actual equipment in place. For chemical API syntheses, the aforementioned layouts are used for this purpose.
For biotechnological API production trains, single-use technology (SUT) is now frequently used, as well as equipment that’s provided by the SUT suppliers for the planners in the form of detailed 2D/3D CAD models.
The functional layout takes all the planning and utility requirements into account.
The entire engineering phase is accompanied by a 3D CAD plant layout that gradually becomes more detailed and grows … and is supplemented during the detail phase with further supplier information as well as drawings (equipment, steel construction and piping).
This is important for the design review in terms of checking that instruments and equipment are accessible for maintenance, inspection and cleaning before proceeding to process plant installation.
A process and technology driven engineering approach
Glatt looks at projects such as the construction of a customised plant for chemical API synthesis from the production point of view: what specifications have to be met?
Which synthesis processes have to be implemented in terms of plant technology? What equipment is required and best suited for this purpose?
This results in technological requirements for the process environment such as plant peripherals and cleanroom design or, if applicable, containment and safety requirements (Figure 5).
Glatt provides all the requisite engineering services, including the layout of the plant, and constructs the necessary buildings, including all interior fittings, until the first batch of active ingredients leaves the factory after successful validation.
Key takeaways
- Even for small batches, modular multiproduct API lines offer flexibility and rapid changeovers at lower investment costs.
- Accelerated planning, procurement and realisation (fast track) using predefined modules leads to time savings and expedites time-to-market.
- Multiproduct lines are not specifically product-optimised; strict cleaning procedures must be implemented.
- When deciding on the concept, the possible future development of the product range should be considered.