Visiting Visp, the manufacturing facility of Lonza in Switzerland, has been hard to forget. It's not the 2-hour train journey through the jaw-dropping scenery of Lake Geneva or the dinner at St. Jodern Wine Cellars by the Heida wine village in Visperterminen (Europe's highest vineyard) that remains in my memory, but the view of the founding location of the Swiss CDMO; living proof of its 123 years in operation. The century-old structures built to house Lonza's quest for calcium carbide (CaC2) applications — the core business at the time — still stand at the heart of the 900,000 sqm industrial compound. The site now also contains 70 labs, R&D and scale-up facilities, and state-of-the-art multipurpose plants, totalling more than 850 cubic metre of production capacity rendered by the work of more than 3,000 staff.
It was a sunny blue-skied autumn day when Manufacturing Chemist visited Visp as part of a handful of international media invited to the exclusive open day event. Guided by high-rank executives, we toured the facility traversing from one building to the next — R&D, microbial, bioconjugates, and the Ibex Solutions building under construction — in the same fashion most Visp workers do: pedalling a bike.
That day, the scientists behind the brand revealed how their teams work, pushing the boundaries of science and business acumen to deliver on the promise of a timely and cost-efficient commercial launch of innovative medicines.
R&D for lead drug candidates
"Over 20% of the molecules that are coming to us now are bispecific antibodies," R&D Director Bernadette Sweeney told us as she presented the Lonza strategy to provide CDMO services for the growing pipeline of complex molecules.
Bispecific antibodies are capable of binding two unique antigens simultaneously, and main applications are immunotherapy and oncology therapeutic areas.
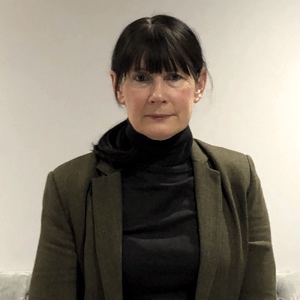
Bernadette Sweeney
R&D Director
Typically, Lonza works with customers once they have selected their lead candidate(s). The Swiss CDMO uses its GS expression platform to generate the production cell line that will be used to manufacture the product.
Lonza's customer base is made of companies of all sizes, including leading biopharma and small SMEs who may not have the know-how or technology to develop a manufacturing cell line and production process in-house.
"With standard antibodies, there is an expectation to go from DNA to investigational new drug application (IND) in 12 months," Sweeney commented, emphasising that clients are now coming with increasingly complex molecules expecting similar timelines. "Often with bispecific antibodies and other novel formats it is a much more complicated process requiring longer timelines and more resources," she explained.
There is yet another hurdle. Sweeney revealed that these novel formats usually don't fit the standard platform process; they require new solutions.
The teams are looking at ways of improving bispecific antibody heavy and light chain pairing to ensure optimal production of the desired product
Improved vector design, host cell engineering, and novel purification and analytical methods are some of Lonza's innovative approaches. Sweeney noted that recent additions to the GS expression system toolbox, the MGV (multigene vectors) and GS piggyBac transposon technology, are being used to enhance complex protein expression including bispecific antibodies.
"MGVs enable up to four genes — common for bispecific molecules — to be packaged into a single vector, allowing gene insertion into the same locus. This process removes the risk of having very unbalanced expression levels of each gene due to differences in transcriptional activity at different loci," she explained.
Pairing MGVs with the piggyBac system, Sweeney pointed out, helps deliver higher yields of challenging proteins. Higher yields are possible, she said, because the system has the capability to insert large DNA cargos (>200 kb) into transcriptionally active and stable areas of host cell genome.
"The Lonza mammalian R&D team is also working with key academics for better understanding of the process inside the cell, in particular the protein folding and secretion and post-translational modification," Sweeney commented. "The teams are looking at ways of improving bispecific antibody heavy and light chain pairing to ensure optimal production of the desired product."
Work on this front continues. Sweeney said Lonza is implementing automation to meet the demand for quick turnaround and lower the cost of development. "By reducing sample volumes and increasing assay throughput, we should be able to make up for some time and costs and deliver a premium product to the customer," she concluded.
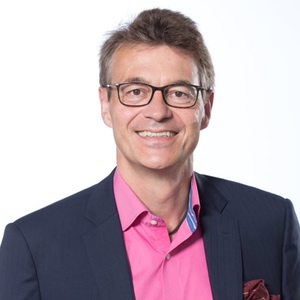
Clemens Jakobi
Commercial Development Director
Microbial manufacturing
Visp holds yet another milestone record in Lonza's history: R&D activities in microbial fermentation began onsite in 1983. It started with developing industrial enzymes, but the know-how quickly became the foundation of Lonza's microbial biopharmaceutical business.
"Escherichia coli (E. coli) was the first expression system used to commercialise biologics, with insulin the first molecule launched in 1982," said Clemens Jakobi, Commercial Development Director, kicking off his presentation.
Jakobi recognised that following the launch of several Immunoglobulin G (IgG) industry blockbusters, the mammalian market has outgrown microbial expression systems. "Around 70% of every kilogram of pharma product today is of mammalian origin, but I believe microbial expression systems will again become more important for biologics manufacturing in the future," he said.
Jakobi pointed to new molecular formats and antibody fragments as an example of the many products that can be created from microbial fermentation. "Microbial expression systems alone can already express antibody fragments with high biologic potency," he said, adding that when more targeted formats are needed, the microbial team join forces with scientists in bioconjugation to create even more potent molecules that can deliver efficacy.
"The technology emerging today is driving a renaissance of microbial expression systems," he said. "We now have the opportunity to manufacture these more complex new molecular formats with microbial expression systems that are also known for their speed, high yields and cost-effectiveness," Jakobi enthused.
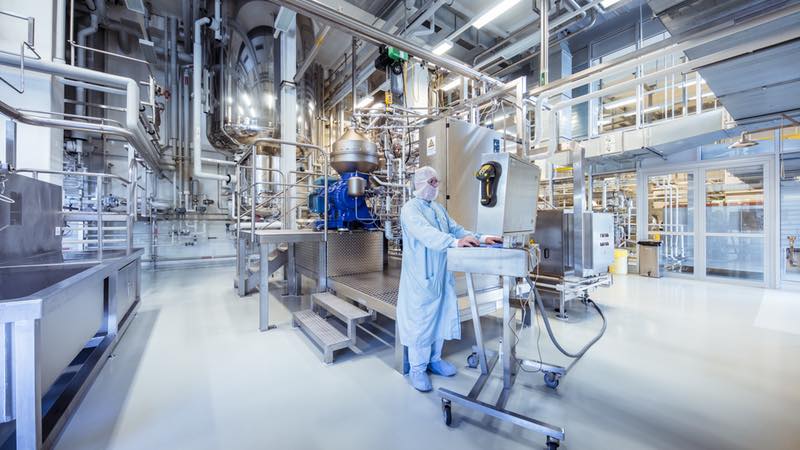
Biologics manufacturing plant
While working with E.coli to produce small quantities of protein is fairly straightforward, to translate that to commercial scale requires a wealth of knowledge. "Companies come to us with a drug candidate in phase I but with a process that is not commercially viable; our development team can optimise it for yields that can be at least 10-fold higher," Jakobi said, noting the team has small-, mid-, and large-scale capacity to bring the molecules through IND into the clinic and on to commercialisation.
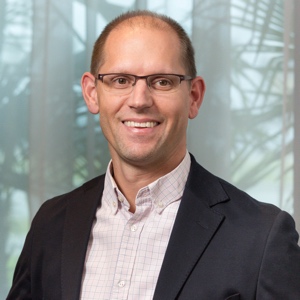
Iwan Bertholjotti
Commercial Development Director
Highly potent bioconjugates
At this stage, it made sense to get to know more about the challenges and opportunities ahead in the antibody-drug conjugates (ADCs) market. Iwan Bertholjotti, Commercial Development Director, led the way and explained some of the intricacies of this segment.
According to Bertholjotti, 60% of ADCs consist of antibodies conjugated with highly potent (HP) payloads, and the toxicity of these drugs requires specific knowledge to handle. The rest, he noted, is non-toxic conjugation, such as microbial antibodies connected to polymers or other substances. "The development and manufacturing of these drugs are often outsourced as it requires specific knowledge that companies may not want to develop in-house," he explained.
A man of numbers, Bertholjotti argued that growth in bioconjugates is expected to reach over 500 molecules in the pipeline by 2024, up from around 270 in 2019. He noted the pipeline of HP ADCs drugs, a subset of bioconjugates, has also grown and seven of these are now approved.
For Bertholjotti, conjugation technology today is more selective, predictable, and safe, hence the higher growth forecast for the next five years. He commented that monoclonal antibodies are successful drugs as they target many unmet needs, especially in cancer treatment. But as ADCs are more complex, the process is often based on trial and error, and there are many challenges to overcome from the supply chain perspective.
Kadcyla, the first ADC approved on the market from Roche, was Bertholjotti's running example for us to understand the complexities of the manufacturing process, and where Lonza expertise lies. "It was our driver to step into this field and build a facility together with Roche in 2006," he said, noting Lonza didn't manufacture Kadcyla's payload, although Lonza does make payloads for other clients.
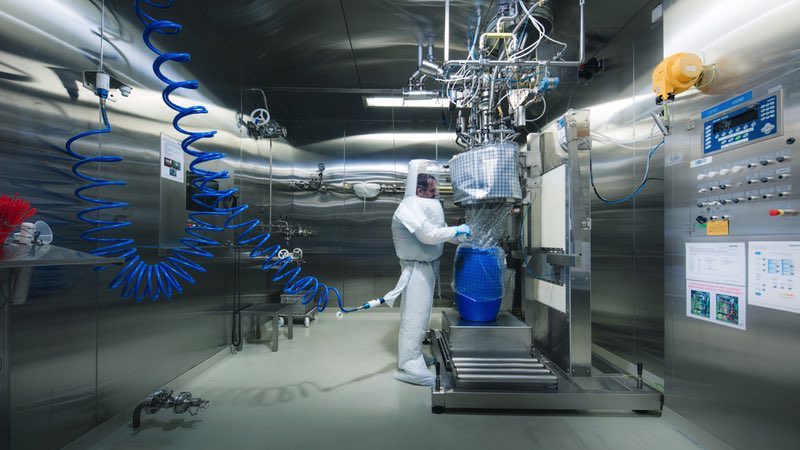
CDMO services include highly potent bioconjugates segment includes the monoclonal antibody,
the highly-potent payload, the linker and the conjugation
Building on the experience with Kadcyla, Bertholjotti illustrated the ADC supply chain. "The toxin was produced in Italy, the receptor in the US and the conjugation was done at Visp. So, we had to freeze the product and ship all the components to Visp. Then we had to conjugate it, freeze the ADC, formulate it and ship it back to the US to make the fill," he noted.
Lonza's offering in this segment includes the monoclonal antibody, the highly-potent payload, the linker and the conjugation. "For the conjugation, you need specific knowledge of biologics and chemistry, and once the molecule is produced, you need the drug product formulation and fill. All these processes are offered at Lonza," Bertholjotti said.
Specific bioconjugation processes are well-established and faster; up to nine months or so. Lonza's executives argued that bringing all the elements of the supply chain under one roof is challenging but greatly benefits manufacturing to commercial scale. Here is where Lonza's Ibex comes to play.
Ibex to the rescue
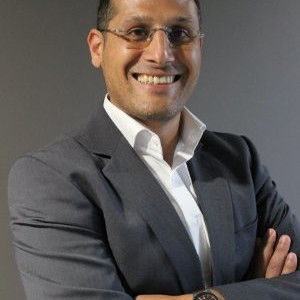
Abdelaziz Toumi, Head of Commercial Solutions for Ibex Design & Develop
"Look at the standard monoclonal antibodies (mAb) we have in preclinical and clinical phases today, and you will find more than 1,070 programmes in the pipeline. We're seeing a growth in biologics of 8-10%." The statement from Abdelaziz Toumi, Head of Commercial Solutions for Ibex Design & Develop, explained the current state of affairs in the pharmaceutical industry and the business case behind Ibex Solutions, the biological development and manufacturing concept that Lonza embarked on since announcing the investment in 2017.
Toumi pointed out that small companies, businesses sometimes made up of a couple of scientists developing a single mAb for the clinic, for example, manage 61% of these early-phase programmes. This segment is huge, he said, and comprised mainly of companies who have no interest in manufacturing themselves.
"Up until recently, these start-ups have tended to use two CDMOs, one for the drug substance and other for the drug product as there were few options. "With this interface, companies may lose time and enter later into the market," Toumi commented as he argued the case for getting them involved in Ibex.
"You need a commercially viable manufacturing process that will take you from IND to the Biologics License Application (BLA), and ultimately to the approval and launch. To achieve that you need to eliminate complex interfaces and simplify the supply chain with one partner who can scale the process so that it is commercially viable." Toumi explained.
Toumi's next argument took on FDA statistics. He said nearly half of all FDA complete response letters contain CMC (chemistry, manufacturing, and control) deficiencies, and that on average, it takes 14 months for companies to overcome the issues and get final approval. "For a start-up, this is a point of no return. You simply invest even more time and money," he said.
The process development lab will be up and running from April 2020
Lonza executives are bullish on what the future holds once the Ibex platform is up and running; the platform incorporates every business unit and expertise from the company. The confidence is reflected by offering clients a 12-month guarantee to bring their molecule from gene to IND ready for clinical phase I, with the added commitment to pay back for every week delay.
"We share the risks," Toumi said. "We do so because we have the GS expression platform with existing knowledge around process development and media selection, which makes us confident in delivering the timeline," he enthused.
Toumi also revealed the commitment is to deliver a minimum of 1 kg of mAb drug substance that can be converted into drug product. "If we miss the 1 kg, we produce it free of charge," he said, and revealed Ibex design is offered at a fixed price package, competitive to the market and convenient for the customer. "There is lots of interest from start-ups. They really like the idea," he enthused, noting Lonza has already signed deals with customers entering in 2020.
Ibex Solutions is a big manufacturing complex. Ibex Design uses half of it, but Lonza is using modular technology for the entire building; thus housing Ibex Develop, for customers working on the launch to market, and Ibex Dedicate, a fully customised commercial supply solution.
At the end of the tour we all agreed on one thing: the pressure is on for operations to begin in the brand-new building. Lonza executives announced that the process development lab will be up and running from April 2020, and manufacturing suites will be operational later this year.