The importance of consistent, high quality coding on packaging or labelling cannot be overstated. Increased globalisation has changed the way many businesses operate, and organisations are functioning in highly complex supply chains wherein misleading information or poor quality codes can have detrimental effects, both for consumers and for organisations. The correct information must be coded onto the right product with 100% accuracy.
Sophisticated supply chain management systems are required to co-ordinate the movement of products between suppliers, retailers and customers.
This advanced technology, such as ERP (Enterprise Resource Planning) or MES (Manufacturing Execution Systems) relies heavily on the creation and longevity of sometimes simple codes on a wide variety of goods and products.
While supplying the right product to the correct location is one function of the code, the other aspects of coding and marking can have a more fundamental and basic purpose.
Customer research conducted by Domino has found that the most commonly required codes are “manufactured on” or “use by” dates, followed by batch traceability and legislative compliance codes (such as food allergens and safety marks). However, code requirements are changing. Within the next 5 years, customers anticipate a higher focus on traceability for brand protection and anticounterfeit purposes, placing increased emphasis on the quality and durability of the printed code.
The advantages of continuous inkje
In high throughput, high productivity manufacturing industries such as beverage, food, life sciences and industrial products, there is a heavy reliance on continuous inkjet printing to create required codes without impacting the speed of production. Continuous inkjet (CIJ) — also referred to as small character inkjet — offers industries a quick drying, non-contact process. The print head is separated from the surface to be printed by a distance of between 5 and 25 mm, before propelling electrically charged ink drops at high speed onto the item, creating a sequence of rounded dots that form a dot matrix code.
The major advantage of CIJ printing is its ability to project ink drops at a significant velocity, from a distance, onto a moving substrate, to achieve very high-speed printing. This distinguishes CIJ from alternative — and potentially higher quality — coding technologies.
CIJ is able to create small codes at incredibly high speeds, in multiple orientations, and onto almost any surface. Originally, CIJ was used to code mainly onto metal, glass, cans, porous or semiporous card and paper. As the packaging industry has evolved, so has the sophistication of CIJ inks. Research shows that new CIJ applications are more heavily weighted to plastics, including flexible packaging, plastic bottles and containers, and plastic mouldings and coatings.
CIJ inks are available in many colours for almost every product and substrate, including speciality inks that can withstand particularly tough processes such as retort and flash freezing, or UV-readable inks for use in anticounterfeiting. This ink range makes CIJ a versatile process for most packaging applications.
CIJ printers are also mechanically robust, able to print for long periods of time and in tough environments before requiring servicing. For its reliability, cost effectiveness and versatility, CIJ is still the tried-and-tested coding technology of choice for the vast majority of applications. For more than three decades, it has imparted health and safety information, helped to move and organise products, and provided brand protection for millions of organisations and consumers.
Challenges for CIJ coding in today’s evolving markets
Although continuous inkjet printing has earned its place and longevity as a favourite coding technology, it has not been the focus of significant technological innovation. Meanwhile, technological advances in manufacturing environments have delivered significant improvements in production techniques, speed and product lines. Likewise, digital developments have resulted in improved traceability and customers expect and demand more information to be made available on their products.
In globalised industries, in which millions of products are moved every year with implications for the health and safety of trillions of consumers worldwide, quality coding is business critical. Poor quality coding has many significant potential ramifications; but, so far, the continuous inkjet industry has arguably failed to keep pace with the industries it supplies.
There are multiple challenges for continuous inkjet: globalised markets create an increased need for traceability and anticounterfeiting; consumer expectations and legislation are increasing the demand for detailed product information on packaging; and inter-brand competition fuels creative on-pack promotion, much of which uses codes as part of multichannel campaign activation. At a practical level, contemporary production environments require all processes to be able to withstand extreme speed and harsh conditions, while the miniaturisation of parts and components in many manufacturing industries requires new levels of coding precision.
Traceability involves marking products in a way that allows them to be tracked through complex interrelated actions, from production through distribution to the point of consumption. The implementation of a coding system has proven to be an effective tool for manufacturers and retailers to maximise productivity and optimise both internal and external supply chain management. This is also where traceability proves to be a practical solution, allowing items or batches to be analysed in a single run or tracked via serialisation codes throughout the supply chain. The rise of counterfeit goods, with the high inherent risks for the health and safety of consumers, has led to more stringent legislation being placed on products, with traceability increasingly becoming a requirement.
An additional challenge is the consumer’s escalating demand for transparency and exhaustive product information, increasingly backed by legislation. For example, many consumer goods must now display allergen and product origination data, requiring more information to be printed clearly and legibly onto a small printable area.
On-shelf promotion is a growing area of brand marketing, often as part of closely integrated multichannel campaigns that make use of variable 2D matrix codes — QR codes — to drive consumers to campaign-specific web landing pages. These codes require a level of precision that can be read by a smartphone camera, historically a challenge for CIJ. Meanwhile, the production environment itself is presenting new challenges for CIJ technology. Thanks to advances in technology, production lines are moving more quickly than ever, producing higher numbers of products, which all need to be coded. For example, a contemporary canning line coding soft drinks produces 6000 cans every minute, or 100 cans of product per second. So CIJ printers must be able to keep pace with the fastest production lines. Technological advances also mean that products may be manufactured in extreme conditions, for example going through retort and snap freezing, as well as being exposed to prolonged periods in damp or dusty production facilities. CIJ codes must have the longevity and durability to withstand the toughest environments and last the lifetime of the product.
In some industries, there is a particular need for ultra-accurate coding placement. For example, electronics products are increasingly miniaturised, meaning that codes too must become smaller and more precise. This is often quite a difficult task for CIJ, wherein the ink is projected onto a fast-moving object. Additionally, often every component of a product is individually coded. For instance, there are 1200 parts in a typical mobile phone, each one with its own individual code so that they can all be traced back to the manufacturer.
While these market and manufacturing trends place new demands on CIJ, the reality is also that many industries are operating with decreasing margins, and are therefore more focused than ever on reducing the total cost of ownership of their technology investments.
The importance of code quality
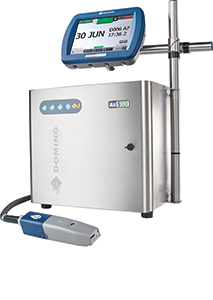
Whereas legacy CIJ equipment may not be able to rise to the various new challenges just described, the positive attributes of the technology mean that many manufacturers continue to operate with CIJ, fine-tuning older printers regularly to optimise performance, and perhaps overlooking substandard coding. However, coding quality is increasingly critical, as an ineffective code means that the code may fail to meet the requirements of the supply chain.
The quality of a printed code relies on several factors: accurate placement, precision jetting, readability and contrast, good adhesion, and durability in the face of environmental stresses and physical handling. There are numerous reasons why a CIJ code could be deemed to be ineffective, including issues relating to the coding system itself and the production environment. Equally, with the introduction of new packaging materials, an inappropriate ink selection for the substrate could result in a poor quality code.
High production speeds can visibly impact the code, resulting in examples wherein the data is not printed within the designated code area, or the code appears to be “stretched” across the label or surface. These errors occur when the products are moving too fast along the packaging line for the printer to keep up with, or if the printer is not correctly set up (distance, angle of print head and so on) to cope with the speed of the line.
Print quality can also be an issue. In some cases, a code’s resolution might not be high enough, which means that more ink drops are required to achieve the desired definition. Furthermore, end code quality can also be affected by poor drop formation in the print head. This results in misplaced drops appearing close to the code, known as “satellites.” If an inappropriate or poor quality ink is selected, then issues of poor adhesion can lead to codes becoming smudged or chipped, making the code illegible. Code contrast can also prove to be a challenge on certain surfaces, such as amber glass or transparent bottles containing dark liquids. Although contrasting colours such as white or yellow are available, their reputation for poor reliability means manufacturers will avoid these inks when possible.
Market research from Domino confirmed that code quality was the most important challenge, both now and in the future. When asked to rate the significance of coding-related issues compared with other production issues, more than half of respondents said that a coding issue would be of the highest importance.
Rewriting the rules of CIJ
With code quality and durability becoming increasingly important, it is clear that technological development of continuous inkjet is needed to deliver optimal drop repeatability, high resolution and accuracy in today’s high speed production environments. The key to solving code quality issues can be found in the print head. If consistent drop generation is achieved, the print head can ensure that no misplaced drops are erroneously printed on the packaging’s surface, eliminating issues such as satellites. More precise drop placement will ensure higher quality coding and enable the creation of smaller, more accurate codes such as 2D barcodes or variable barcodes, the use of which is predicted to rise significantly in the next 5 years.
Ink plays such a critical role in the process, and best CIJ performance requires control over ink pressure, temperature and viscosity. Improved consistency and control of ink flow will also have the effect of reducing ink build-up in the nozzle, minimising line stoppages and improving productivity. A comprehensive range of ink is also essential to ensure best market coverage, reliability and performance. As CIJ systems are used in so many different areas, some of which are classified as harsh environments, a variety of inks is needed for specific industries, whether it is EuPIA GMP and Swiss List-compliant inks for the food, beverage and life sciences sectors, or heavy duty inks for industrial manufacturing. Inks are also needed that will adhere reliably to complex surfaces, even long after harsh post-print processes such as retort and blast freezing.
To be fit for the future, CIJ systems must be robust enough, from the print head out, to withstand challenging production conditions for maximum productivity with minimal downtime. They must also be easy to operate and maintain for low cost of ownership, without compromising overall equipment efficiency. For example, the print head should be resistant to contamination to minimise cleaning requirements, even when using pigmented inks. The CIJ printer should also be able to withstand washdown conditions, while protecting against steam and the assorted contaminants that may come into contact with the system.
Revisiting the original science of the ink drop
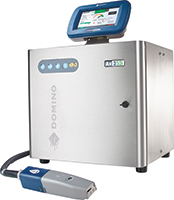
Reflecting the current and future requirements of the market, and the technological capabilities needed to address them, Domino Printing Sciences offers the Ax-Series, a new range of continuous inkjet printers optimised for the most demanding industrial environments. In developing the new series, Domino has rewritten the rules of coding and marking by revisiting the underlying science behind CIJ and introducing innovations in three key areas. This has resulted in a comprehensive re-engineering of CIJ technology that will reset customer expectations of productivity, quality and cost of ownership. Domino’s three pillars of innovation across the Ax-Series are:
- the new i-Pulse print head and inks: i-Pulse controls individual ink drop formation, delivering significant advances in droplet accuracy, placement and ink usage for reliable, high-speed and consistent code quality
- the i-Techx electronics and software platform, designed to optimise lifetime return on investment and eliminate coding errors by enabling smooth integration into the production line and service support environment.
- Domino Design, a fresh approach to the total product design to maximise productivity and ease of operation, delivering printers that are robust and reliable in the harshest environments.
The innovations in the Ax-Series are the result of extensive R&D and collaboration with Domino customers in a broad range of industries. By redesigning CIJ technology from the ground up, Domino aims to enable customers to achieve the high level of code quality required for their business, with a coding process that is familiar and proven in practice.