As drug manufacturers increase their global reach, fast and safe distribution of temperature-sensitive drugs is a key issue. Christopher Dehio, Lufthansa Cargo, assesses the pharmaceutical airfreight market and its challenges.
When we in the airfreight business talk about market sizes for a particular product, we are mostly interested in the weight or volume that needs to be transported. However, most of the statistical data available to describe the pharmaceutical market is in terms of value produced or values sold. Both show impressive growth figures and you could be led to believe that similar growth in transportation requirements must therefore also apply. Unfortunately it is not quite so simple.
While values produced or values sold give a solid indication of how healthy the ‘health market’ really is, neither has real significance in determining market sizes for the global, cool-chain air logistic industry and would lead to incorrect conclusions. For instance, the introduction of a more stable generic may lead to higher sales volumes but could also make cold chain transportation altogether unnecessary.
The significance of weight – or volume – for the air freight industry can be best shown with the example of India: when we look at value exported, India would account for only 2% of the total value exported worldwide. However, looking at the weight exported, India is – after the European Union – the second largest exporter of pharmaceuticals. In comparison, Canada ranks 4th by value but only 30th by exported weight.
Most of the statistical data available to describe the pharmaceutical market is in terms of value produced or values sold. Both show impressive growth figures and you could be led to believe that similar growth in transportation requirements must therefore also apply. Unfortunately it is not quite so simple
If we turn to growth factors to determine the temperature-sensitive air freight market we should also look at the growth of exported pharmaceuticals by weight and not values or production volumes. Take, for instance, the CAGR of the six leaders in export. India again plays a very significant role – not only is it the second largest exporter of pharmaceuticals, it also has the largest growth rate in pharma exports. But the relevant portion for the air freight business still is not clearly identified.
A closer look at European trade statistics (Eurostat) reveals that sea and road transportation of pharmaceuticals is clearly the favourite option. Only 18% of Europe’s exports are carried by air. However, one thing is for sure: when it becomes valuable, it goes by air. Some 57% of the entire value exported from the EU is moved by air, whereas the entire sea transportation – which by weight is two and a half times more than air – makes up only 20% of the value. That obviously puts the question of the liability risk for the air carriers on the table.
temperature deviations
Were it not for the various international legal tools available to the airlines to limit their liability, it is doubtful that any carrier would accept shipments of which they know neither the value nor the sensitivity of the contents, and where a total loss could be incurred by a temperature deviation of a mere few degrees from a given set point. But airlines do know that a shipment of pharmaceuticals is the result of an expensive and complicated production process and that the products are destined to end up in the human body, to achieve the desired patient outcome. The value of the goods transported often rate as much as 300 to 400 times the shipment revenues that can be obtained.
So avoiding temperature deviations in the first place is the top priority. Not only because those involved in the logistics chain have made promises or would like to avoid financial complications, but also – and perhaps mainly – because we all have a moral obligation to see that nothing goes into a human body that might have deteriorated from its assigned properties, just because of a temperature variation during the transit period from production to consumption.
In that context, understanding what an air carrier can do and what it cannot do is a first but important step to help avoid temperature excursions. The answer to the question: ‘What can we do to improve the efficiency of the air transportation part?’ might well be: ‘understand where the limitations are and adjust our packaging solution appropriately’.
Ever since the old DC3 plied the South Pacific, temperature-controlled transportation was the thing for airfreight and one might expect the airlines to have temperature control – under control.
After all, aviation is – and always will be – at the forefront of technological development: it is a very process-driven industry with a high level of built-in, redundant safety measures and, above all, is fast and reliable. But the air transportation part is not what differentiates one airline from another. They all fly at the same speed; they all use the same or similar equipment. One airline’s 747 does not differ much from the next airline’s – at least not technically.
But what happens on the ground before and after the flight is decisive. How good are an airline’s processes on the ground and how well do they control those processes? Can they provide the same level of protection at all destinations in all four corners of the world?
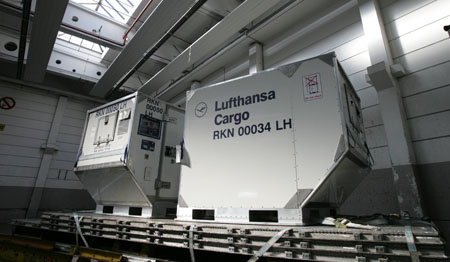
What happens on the ground before and after a flight is key to product stability
To that end, Lufthansa Cargo has been working to perfect its cool chain transportation processes continuously for 10 years or more. Apart from utilising equipment that was available on the market, together with its partner DoKaSch, Lufthansa began perfecting the design of climate-controlled containers that had integrated electronic feedback loops that could actively control the temperature, using dry ice as a cooling agent. These then developed further to include heating capabilities and finally compressors that would by far surpass the technology available at the time. Since then, both passive and active packaging technologies have been going through an impressive development.
Apart from investing in container technology, Lufthansa Cargo also invested in upgrading the infrastructure at Frankfurt Airport. In January 2011, Lufthansa Cargo inaugurated its new, state-of-the-art pharma warehouse, the Lufthansa Cargo Cool Center. Covering an area of more than 45,000ft2, it contains four temperature-controlled areas and is probably the only one in the market that is owned and operated by an airline.
Air carriers will provide procedures that support temperature-sensitive passive shipments on the ground, but they have little control over the duration of ambient temperature exposures
While passive packaging can be more affordable, depending on the business case, temperature variations can and do occur. Passive packaging is subject to ambient temperatures just as active containers are. But unlike the active containers, they have no technical components that control the temperature through a signal feedback loop. While insulation and gel-packs help mitigate the risk of temperature deviations, they don’t eliminate them. And although the cargo holds of an aircraft are pressurised and heated, temperature control in the sense that the pharmaceutical industry is used to, does not exist. Since the air carrier has no knowledge of how sensitive the contents really are, it is usually left up to the shipper to determine which packaging type would be appropriate for the sensitivity of the contents and the intended transportation profile.
Air carriers will provide procedures that support temperature-sensitive passive shipments on the ground, but they have little control over the duration of ambient temperature exposures. Shipments must be taken from the aircraft and moved to warehouses. On busy hubs, this can take quite a while and tarmac exposure can be extreme.
Warehouses themselves are designed for transit, not for long-term storage. They are designed for a high throughput, so doors open and close all the time. Hot or cold shipments come in off the tarmac and are put into a temperature-controlled environment where they either absorb or release energy, depending on the length of time that they have been exposed to outside temperatures. That makes precise temperature control of an air cargo warehouse a challenging task.
limiting factors
Factors such as weather or even geophysical incidents (volcanic eruptions, earthquakes), but also interruptions by labour disputes, traffic congestion and technical deficiencies at airports or with the aircraft itself, can make deviations from standard procedures necessary and can have an impact on the stability of the temperature range of a given packaging solution. It is for precisely these reasons that many countries have mutually agreed to limit the liability of a carrier.
Ground-breaking, revolutionary ideas seem more likely to develop in the area of active temperature-controlled containers
But it is not that airlines do not have more reliable solutions available: as far as active temperature control is concerned, the solutions are quite sophisticated and rarely fail expectations. The high-end compressor technologies have a greater reliability but they also require higher investments and must therefore achieve higher rates in the market.
The future of precise temperature-controlled transportation most probably lies with further innovations in active temperature-controlled packaging solutions. It is likely that passive packaging solutions have reached the pinnacle of their development.
Ground-breaking, revolutionary ideas seem more likely to develop in the area of active temperature-controlled containers. Here the number of sensors will be increased in the near future to record other potential threats to the molecular integrity of the pharmaceuticals.
Factors such as shock, vibration, X-rays, altitude and radiation may have an impact and might have to be measured and recorded. The availability of GPS/GSM technology will make real-time data logging available and help airlines to intervene pro-actively before things go wrong. The development of an airworthy hydrogen fuel cell will give active containers vastly improved independence from external power sources. New lightweight composite materials will make containers lighter and better insulated.
But there are a few simple things that can be done before sending a temperature-sensitive shipment on its way:
- Anticipate significantly varying temperatures and choose appropriate packaging
- Deliver and pick-up as close to the flight occurrence as possible
- Put temperature recorders inside the packaging and not where they are exposed to sunlight
- Clearly label all packaging units with unambiguous labels
- Avoid long storage periods at airports
- Ensure all import and export documentation fulfill all country regulations
But until the ultimate, fail-proof packaging technology has been developed – one that you can pack, turn on and forget – the best plan to avoid temperature excursions is for the shipper, the forwarder and the carrier to come together and openly discuss the needs and capabilities of each party involved. Without this tripartite exchange too many elements of the supply chain will be left open to guesswork and assumptions in a complex logistical challenge that leaves very little room for error.