Downtime is a word that every pharmaceutical manufacturer dreads. Some are so fearful of it, they prefer not to even say the world out loud, merely referring to it as “the thing that shall not be named.”
Okay, that might be an exaggeration, but it’s fair to say a head-in-the-sand approach is very rife when it comes to talking about one of the major causes of downtime. In the shiny world of pharmaceutical manufacturing, there is one word that people really don’t like to hear: obsolete.
Advocates of Industry 4.0 and the IIot (Industrial Internet of Things) promise a future of self-analysing, hyperconnected machines that tell you when they are about to have a breakdown and preorder the parts to fix themselves. That may well be the way things are going, but where does it leave the vast majority of machinery bought and installed before the revolution?
The truth is that all machinery is set to become obsolete at some point. It’s the nature of the physical world that things wear out. The march of time simply cannot be stopped. We understand this about ourselves and make plans for our own retirement. When it comes to us, extended quality of life can come from careful planning while we’re still fit and well.
In industry, by contrast, a recent global study showed that the majority of companies have experienced at least one unplanned downtime outage during the past 3 years, costing an average $260,000 per hour across all businesses.
The Vanson Bourne global study, sponsored by ServiceMax, from GE Digital, surveyed 450 field service and IT decision makers in the UK, US, France and Germany across the manufacturing, medical, oil and gas, energy and utilities, telecoms, distribution, logistics and transport sectors.
As well as estimating downtime losses to be, on average, $2 million per year for 82% of businesses, it also concluded that around 70% of companies lack full awareness of when their equipment is due for maintenance, upgrade or replacement.
So where does this leave the pharmaceutical manufacturer who doesn’t have the budget, or the inclination, to overhaul its entire line? The answer is that it’s all about planning. A good obsolescence strategy will ensure you get the maximum value from previous or new capital investments in terms of ongoing productivity, performance improvement and energy efficiency.
Lifecycle
Step one is to understand that parts and spares prices have a lifecycle. They start at a fair price; then, as machinery starts to reach obsolescence, they rise dramatically as parts become hard to find; later, they drop even more dramatically as original equipment starts to be replaced.
Small and medium-sized businesses who cannot easily afford to overhaul capital equipment can, however, make use of falling prices and avoid disruption and downtime if legacy equipment is well maintained. The Internet has opened up the spares market, so companies can implement a spares strategy that does not necessarily rely on the OEM.
Having an obsolescence strategy at the outset can help companies to avoid buying spare parts at peak prices and avoid the costs of disruption from stress purchasing — such as when equipment has already broken down.
Risk analysis
Conducting an Obsolescence Report and a Risk Analysis is a good first step toward developing a full strategy. Risk planning is best done on a rolling timeline using an inclusive framework that accommodates any factors that could contribute to the likelihood and potential impact of obsolescence.
A usual starting point is simply to identify critical assets and then assess the risk of obsolescence in both qualitative and quantitative terms.
Once the risks have been identified in relation to each asset, the next step is an assessment of obsolescence likelihood. Data for this can be gathered from everything from the maintenance logs and internal systems to the reliability of the supplier in terms of SLAs, service and support. By looking into a supplier’s end-of-line (EOL) plans, manufacturers can mitigate the risk of discontinued support or technology upgrades.
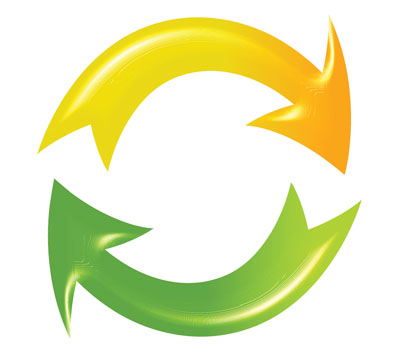
Strategy
Once you are aware of the risks, a three-part strategy can be developed to minimise the overall obsolescence risk.
Repairs: Assess what can be repaired in the event of a breakdown. Can you wait for a repair? For items that cannot afford any downtime whatsoever, a repair may not be an option as this is going to take a minimum of 24–48 hours — and that’s if the repair supplier has the components in stock needed to complete it.
For items such as HMIs, for which very specific overlays are required to complete the repair, lead times can push timescales into weeks rather than days ... so repairing every item is not always an option.
Who will do the repairs? What resources do they have? Do they have a good track record? Is the company you’re looking at hiring actually going to do the work or outsourcing it? A quick company check will help to narrow down the list of suppliers. Check on Google maps if their office is capable of doing repairs and/or check LinkedIn to see if they actually have the staff required.
Upgrade: Upgrading in the middle of unplanned downtime is never recommended, so it’s worth considering whether the equipment can be upgraded. What equipment can be upgraded? What equipment should be upgraded? When should it be upgraded? Simply having a plan to answer these questions will help keep you ahead of the curve.
Owing to their rarity, the cost of some obsolete parts can actually be more than double the cost of a modern equivalent. New equipment comes with a warranty and is more readily available, so you can be confident that you will receive ongoing support for a number of years.
Aside from these benefits, you can also get other benefits such as increased machine productivity, throughput and reliability. Upgrading can help to reduce energy costs and therefore save more money. You should always consider these benefits as they can make the payback period on improvements seem really quick.
As the majority of applications are relatively straightforward and require only minor wiring modifications, AC drives are often a prime candidate for upgrading. For more complex applications, there can be a reluctance to upgrade in a breakdown situation.
It is often easier to go like for like, but this isn’t always the best option. A good supplier should have the necessary skills to assist or even set up the replacement before shipping. Planning the upgrade in advance is always the best solution.
Spare parts: What spare parts will be needed? Do we have them in stock? Keeping a good stock of the right spare parts can help to mitigate the risk of breakdown disasters and expensive downtime. If a repair or upgrade is not an option, but the part is critical to your production, a spare should be kept in your stock so that, in the event of a breakdown, you can switch out the faulty unit in a matter of minutes.
This mitigates downtime and gives you the option to repair the faulty unit and put it back into your stores, reducing future costs on spares management.
Buying spares at the right time can save you a lot of money compared with purchasing when you are already on breakdown and factoring in express shipments from wherever the part might be in the world — as well as the unit itself possibly being a lot more expensive because of its rarity now that it’s obsolete.
In summary, a step-by-step obsolescence plan is essential to avoiding the terminal risks of downtime. There is no silver bullet ... but a combined and forward-thinking approach should deliver benefits.
NB: This article will appear in the March 2019 issue of Manufacturing Chemist. A recent digital edition is available online.