Choosing the right flowmeter from the dozens of types available is difficult. Paul Trevitt, of Burkert UK, provides a few insights.
There are so many different flow measurement solutions on the market today that discussing all the potential options is an impossible task. However, as with all technologies, some designs of flowmeter are more widely used than others. In this article we look at five of the most popular units, discuss their advantages and disadvantages and highlight their major areas of application.
The five types include: paddle wheel, differential-pressure, mass, Coriolis and oval-gear. The choice of a particular unit for a specific application depends upon a number of parameters, including medium type (gas or liquid- viscous, free-flowing or aggressive), operating temperature and pressure, pressure drop, accuracy repeatability and cost.
Paddlewheel flow meters are probably the best known type: their technology is widely established, and they are among the lowest cost devices available. They can be used on fluids, including viscous and corrosive liquids. However, their susceptibility to variances in viscosity, which often causes error, means that they are unsuited to highly precise measurement applications.
Typical applications for paddlewheel flow meters include: monitoring chemical lines, filtration loading and flow in material blending applications, measuring water flow in process plants or laboratory facilities, and monitoring supplementary water for food & beverage plants.
With a wide variety of flow ranges and models for liquids, the paddlewheel meter is one of the most versatile designs on the market. However, they cannot be used with viscous fluids or those containing solids or entrained air bubbles. They are generally reserved for use with clean liquids because of the possibility of minute particulates becoming lodged in their moving parts.
Mass flowmeters are one of the most popular gas-measurement technologies in use today. In common with paddlewheel flow meters, mass flowmeters are in the middle cost range, and they have no moving parts. But unlike paddlewheel flow meters, they are suitable for use on gases. Until recently this would have been clean gases only, but new FlowCapillary sensor technology, developed by Burkert for use in its 8710/8700 mass flow controllers, enables the device to be used also with aggressive gases, due to the isolation of the sensor technology from the gas flow path.
A key benefit of mass flowmeters is that, because they measure mass flow rather than volumetric flow, their operation is generally unaffected by fluctuations in line pressures and temperatures. This is important for the users, because when piping expensive gases, it is certainly more cost-effective to keep track of the amount of gas used based on mass, rather than volumetric flow.
Coriolis flowmeters employ an inertial force discovered by 19th-century mathematician Gustave-Gaspard Coriolis and are among the most accurate available today, a feature reflected in their high price. Like mass flow meters, Coriolis based devices offer the key advantage of measuring mass flow instead of volumetric flow. However, unlike the mass controller, Coriolis units work with both liquids and gases – including corrosive gases and viscous liquids. Because mass is unaffected by changes in pressure, temperature, viscosity and density, reasonable fluctuations of these parameters in the fluid line have no effect on the accuracy of the meter, which can approach 0.05% of mass flow.
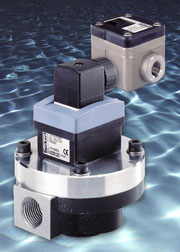
Burkert 8070/8071 flowmeter
Typical applications for Coriolis flowmeters are blending ingredients and additives, monitoring concentration and solids content in liquids, general-purpose gas or liquid flow, performing primary checks on secondary flowmeters, metering natural gas, and monitoring fluids such as syrups, oils and suspensions. However, care must be taken when using Coriolis meters with viscous substances, because pressure drop can increase and become unacceptably large as fluid viscosity increases.
Whereas Coriolis flowmeters can be used up to a point with viscous liquids, oval gear flowmeters are designed specifically for use at high viscosities. For example, meters such as Burkert's new 8070/8071 units provide precise and reliable flow measurement of high viscosity fluids (glue, honey and oil) at up to 1- million centipoise.
The 8070/71 devices are designed with a pair of meshed (geared) oval rotors that rotate under fluid pressure in an engineered measuring chamber. This arrangement, with precision stainless steel (PSS) gears and FKM seals as standard, is characterised by its high levels of reliability, its ability to be used on horizontal, vertical and gravity applications, and its accuracy, which is better than 0.5% of reading on larger models.